Warehouse stock management: orchestrating automation without losing control
- 30 April 2025
- Exotec’s Paul Renou and Manhattan’s Marco Klaassen
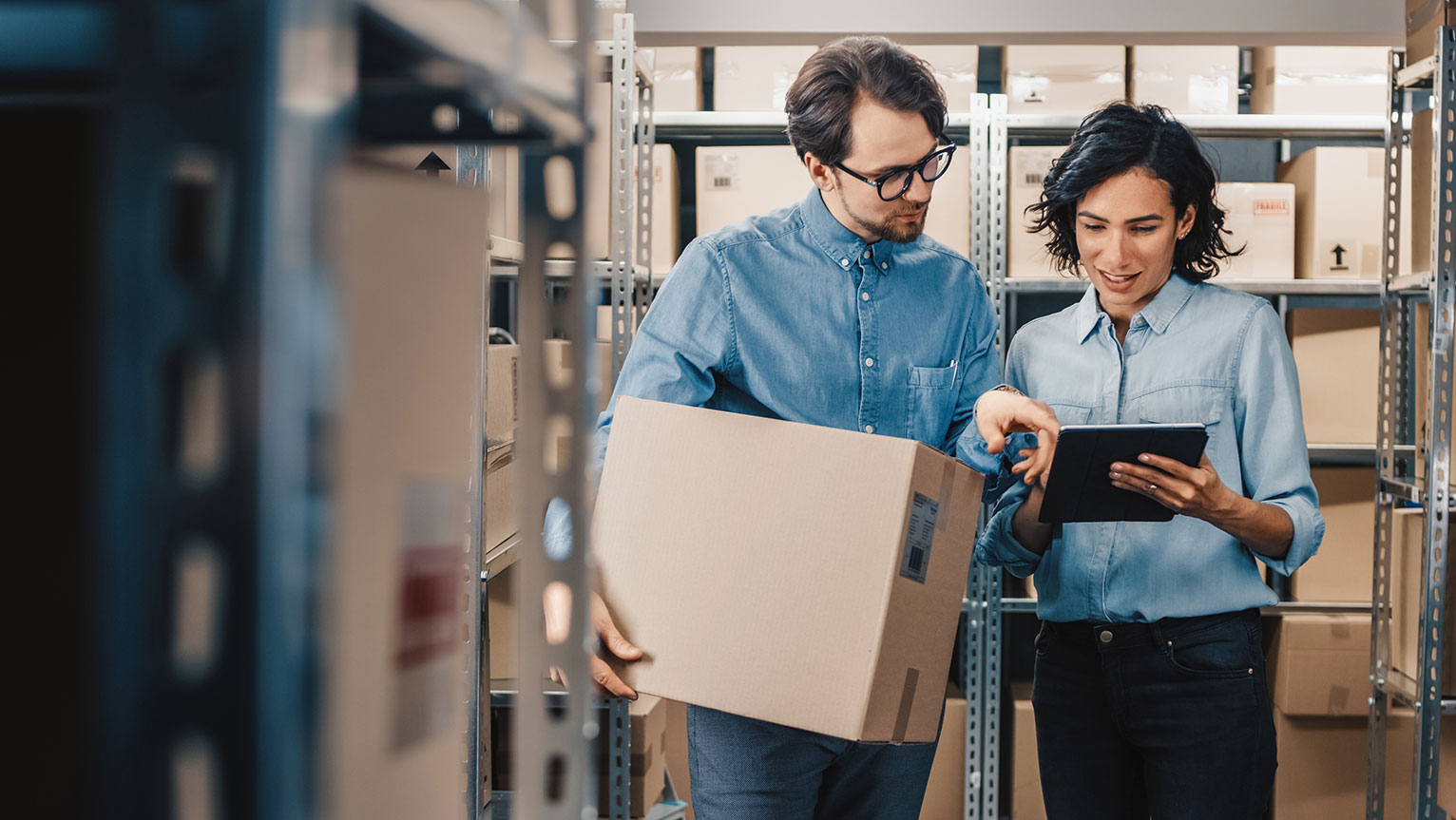
Managing inventory across a warehouse is already complex — but when manual operations, automation systems, and robotics are all in play, that complexity multiplies. How do you maintain real-time stock accuracy across such a fragmented environment? How do systems communicate clearly and reliably? And what role does data play at the core of it all?
To explore these questions, Exotec’s Paul Renou spoke with Marco Klaassen, Senior Director of Professional Services at Manhattan Associates. His insights build on the foundation laid in Exotec’s earlier discussion with Manhattan’s Rémi Coolen, Director of Business Solutions, who outlined how to implement a continuous data quality strategy — a topic closely tied to stock accuracy. (Read that article here: Data quality: an essential for your warehouse).
From orchestration layers to integration logic and predictive tools, this article dives into how Manhattan’s warehouse management system (WMS) tackles the everyday realities of inventory control in modern warehouses.
Real-time accuracy as a baseline requirement
In hybrid logistics environments where human operators work alongside goods-to-person robots and automated systems, stock accuracy is non-negotiable. At Manhattan, reliability depends on a clear allocation of responsibilities: the WMS manages manual operations, while automated systems retain control over their own inventory.
“For manual operations, Manhattan is the inventory master. For automated systems like Exotec, it’s the other way around: the automation system is the master, and Manhattan is the secondary,” explains Klaassen.
Synchronisation is ensured through regular inventory snapshots sent by the automation system. These are compared against the WMS reference and adjusted if needed. The results are then transmitted to the customer’s ERP, maintaining end-to-end consistency.
The vital integration layer: the role of the WES
Between the manual and automated worlds, the warehouse execution system (WES) acts as a smart interpreter. This integrated module allows the WMS to communicate with automation systems by adapting message formats, protocols, and content.
“The WES allows us to ingest or emit flows to and from various systems — whether it’s Exotec or a parcel sorter — by adapting to the specific communication formats and protocols of each,” Klaassen summarises.
More than just a technical connector, the WES embeds operational logic as well, enabling, for instance, the balancing of load between different systems or adapting the warehouse’s behaviour to context.
Three levels of orchestration, clearly defined
To clarify the roles of each layer, Manhattan defines three functional levels. First is the management layer, where the WMS decides from which zone to retrieve inventory. Then comes the execution layer, managed by the WES, which orchestrates available resources. Finally, the control layer is handled by warehouse control systems or programable logic controllers, which execute physical tasks.
“This third level, control, is something Manhattan does not do. But at the execution level, there can be some overlap — solutions like Exotec already orchestrate their resources very effectively,” notes Klaassen. In such cases, Manhattan intentionally delegates orchestration to avoid compromising system performance.
Integration is no longer a technical hurdle — it’s semantic
Whereas a decade ago integration was often hindered by incompatible protocols, modern systems are converging around common standards such as REST APIs and JSON, significantly easing communication. Yet, some challenges remain.
“The real challenge now is understanding the data we exchange,” warns Klaassen. Misinterpreted data — even if technically well formatted — can lead to stock discrepancies that are difficult to detect.
Cybersecurity is another growing concern, particularly given Manhattan’s native cloud architecture. “Not long ago, we faced challenges integrating with on-premise systems due to security concerns. That’s no longer the case — things have evolved a lot,” Klaassen adds.
Fixing errors — or better yet, preventing them
When stock errors do occur, Manhattan provides a suite of corrective actions: cycle count tasks, real-time inventory updates, or local reconciliation. But prevention remains the priority.
“We always start by securing the inbound flows. If data is accurate at the point of entry, there are fewer problems downstream,” Klaassan explains. This preventative approach includes reinforced checks for high-risk suppliers and rule-based automation to trigger verification tasks when anomalies are detected.
Stock allocation designed for efficiency
The WMS can be configured with dynamic allocation strategies: prioritising small quantities to free up space; grouping picks in a single location; following the first in, first out principle or expiration rules; and more. “Some strategies are customer- or channel-specific. And we can even adapt them throughout the day,” says Klaassen. This flexibility allows warehouse operations to align continuously with changing priorities and constraints.
Data quality: the foundation of any logistics strategy
Klaassen is clear: “If products aren’t measured correctly or are mislabelled, everything else collapses.” The goal is not only to ensure initial data accuracy, but also to guarantee ongoing data integrity.
Manhattan offers user-friendly input interfaces, mobile tools, and supplier key performance indicators (KPIs). These tools help transform data from a potential weak point into a reliable operational asset.
Adapting in order to anticipate
The WMS’s flexibility also makes it possible to react to workload shifts or disruptions. When an automated system reaches its capacity, the WMS can reroute flows to alternative zones. “It’s essential to have a holistic view of the warehouse and to treat manual areas as intelligent buffers,” says Klaassen. This real-time adaptability depends on unified inventory visibility and dynamic resource planning.
The right metrics to drive performance
For Klaassen, three KPIs are essential: inventory accuracy, order fill rate, and stock turnover. To these, he adds a fourth that is often overlooked: carrying cost. “Keeping a pallet in storage for two months instead of one week has a cost. And that cost becomes critical when space is limited or when temporary storage must be rented,” Klasseen notes.
Orchestrating complexity through open architecture
In an automated warehouse, stock management is no longer just about tracking ins and outs. It becomes a matter of orchestration, where every system is treated as an autonomous resource within a larger logic. Klaassen concludes: “Performance doesn’t just come from technology — but from how effectively it integrates and works with the broader ecosystem.”