Resources and Insights
Get insights into the latest happenings at Manhattan or filter content to learn more about a specific topic.
Featured
The Road Ahead: Unlocking the Future of Transportation Management
Explore what 1,450 global supply chain leaders are prioritizing and uncover the trends shaping transportation through 2030.
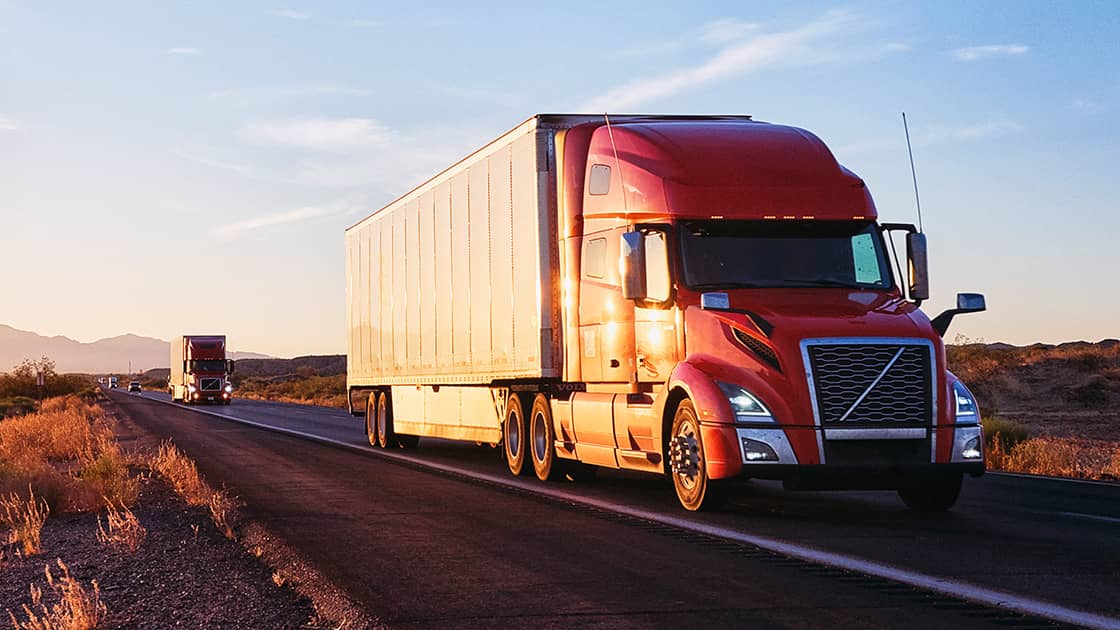